Electric Flight Terminology
July 1, 2000 for Sailplane & Electric Modeler Magazine
In this installment, instead of discussing a particular topic, I’m going to present a glossary of commonly used electric flight terminology. There are a lot of buzzwords flying around in this hobby which can be very confusing to the e-flight beginner.
Unlike a normal glossary, which is arranged in alphabetical order, I’m going to start with some general terms, and then work my way from the front of a typical electric plane to the back. I’ll stop just before we get to the battery, because there’s enough terminology there to fill up another whole installment in which we can explore this area in the detail it deserves.
Author’s Note: Some additional terms have been added since this article first appeared, and I’ll be adding more over time. I also plan to add photos to go with some of the definitions.
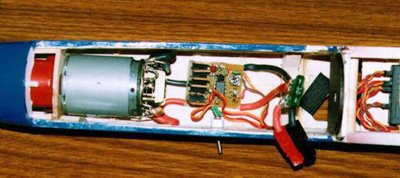
A typical electric power system installation, starting at the front with a folding propeller, gearbox (only partially visible due to the cowling), ferrite motor, high-rate electronic speed control, 30A fuse, and Sermos connectors (hanging over the edge of the fuselage).
General Terms
These terms describe electrical concepts or general electric flight concepts. Although you don’t need to be an electrical or electronics whiz to be successful at e-flight, a basic understanding of these concepts can make things easier for you.
Current (Amps)
Current is what makes electrical things go. It is the word used to describe the movement of electrons through a wire or other conductor. Introductory electrical textbooks often make an analogy between electrical current and the flow of water through a pipe. Current is measured in Amperes, often abbreviated to "Amps" or "A". The symbol for current in electrical equations is "I".
Voltage (Volts)
Voltage can be considered as the electrical equivalent of water pressure. Without pressure, no water will flow, and hence, there will be no current. Voltage is measured in Volts, abbreviated to "V". The symbol for voltage in equations is also "V".
Resistance (Ohms)
Resistance is opposition to current. Using the water analogy, it is a restriction in the water pipe. Resistance is measured in Ohms, abbreviated to the Greek letter "Ω". The symbol for resistance in equations is "R".
The three quantities of current, voltage, and resistance, are related by Ohm’s Law, which states that voltage equals current times resistance (V = IR). This can be rearranged to I = V/R or R = V/I as necessary when solving electrical problems. Think how this might apply to a water system (hint: a smaller pipe is equivalent to a larger resistance).
Power (Watts)
Power is the ability to do work, a concept not unique to electricity. In the electrical world, it is the current times the voltage (P = IV). As with water, the higher the pressure (voltage) or the higher the flow rate (current), the more power is available. Power is measured in Watts, abbreviated to "W". The symbol for power in equations is "P". In North America, non-electrical power is often measured in Horsepower, one of which is about 746 Watts.
Another important equation involving power is P = I2R which states that the power consumed by a resistance is the square of the current, times the resistance.
Efficiency (%)
In its most general sense, efficiency is the ratio of output power to input power. For example, a motor might be 75% efficient, which means that only 75% of the electrical input power (voltage times current) is usable to do work at the output shaft (such as turning a propeller). The rest is wasted as heat, noise, or light. There is also the concept of system efficiency, which is the ratio of output power to input power of an entire system (not just the motor).
Wire Gauge
This is a measure of the cross-sectional area of a wire. The most commonly used wire gauge system in North America is American Wire Gauge (AWG). In this system, the higher the gauge, the thinner the wire. Going down three wire gauges (e.g. from #16 to #13) represents a doubling of the wire’s area. The resistance of a length of wire is proportional to its length, and inversely proportional to its area, so thicker and/or shorter wire will have less resistance, and hence waste less power on the way to the motor.
Power Loading (Watts per Pound)
This is our first electric-flight specific term. It is simply the power available, divided by the weight of the aircraft. Usually, input power (current times volts as measured at the battery) is used, although it is really output power (power turning the propeller) that is more important. An input power loading of around 50 Watts per Pound (W/lb) is considered adequate for trainer-like flight with mild aerobatics (assuming a motor efficiency of about 75%).
The Business End
Folding Propeller
A folding propeller is one in which the blades can fold back against the sides of the plane when the motor is stopped in flight. This has the effect of reducing drag and improving a plane’s glide (especially desirable for electric-powered sailplanes). A folding propeller is also less likely to break during a bad landing, hence some people (somewhat cynically) refer to them as "pre-broken". Never use a folding propeller on a glow engine; the blades will come off.
RPM
A measure of rotational speed of a motor or gearbox output shaft. RPM is short for "revolutions per minute". Roughly speaking, a motor turns voltage into RPM.
Torque
This is a measure of the amount of turning force on an output shaft, and is usually measured in inch-ounces. Again roughly speaking, a motor turns current into torque. The RPM times the torque is a measure of the motor’s output power.
Gearbox
A gearbox is used to trade RPM for torque by turning its output shaft at a lower RPM than the motor’s output shaft. By increasing torque and reducing RPM, the same motor can turn a larger propeller, albeit more slowly. Since larger propellers are more efficient than smaller ones, more power becomes available to fly the plane.
Pinion and Spur Gears
The pinion gear is fastened to the motor shaft, either by a friction fit or by a small set-screw. The spur gear is fastened to the gearbox’s output shaft. The gear ratio is given by the number of teeth on the spur gear divided by the number of teeth on the pinion gear.
Motor
Electric models use motors, whereas internal combustion models use engines. A motor converts electrical energy into mechanical energy, whereas an engine converts thermal energy into mechanical energy.
Motor Constants
Motor constants are numbers used to describe the characteristics of a motor using a few numbers. These constants are useful for predicting motor performance under various conditions. The most commonly used constants are RPM/volt, no-load current, and internal resistance, designated by KV, IO, and RA respectively.
Ferrite Motor
A ferrite motor is one whose magnets are made of an iron-based compound (usually very fine particles of iron suspended in a ceramic base). Ferrite magnets are inexpensive and used in the vast majority of small permanent-magnet motors. Examples of ferrite motors are the Graupner Speed series and most R/C car motors (Kyosho, Trinity, etc.).
Cobalt Motor
More powerful and durable magnets can be made out of an alloy of samarium and cobalt. Such magnets are used in the more expensive and better quality model aircraft motors, such as those from Astroflight. The better magnets make for a more efficient motor.
Armature
The armature is the part of the motor that turns. It is fastened to the motor’s shaft. The armature has three or more poles which are wound with wire to produce magnetic fields.
Turns or Windings
The number of times the wire is wound around each pole of the armature is called the number of turns or windings. Some motors are wound with two, three, or four parallel strands of thinner wire instead of a single thick wire, known as a double-, triple-, or quad-wind, which is independent of the number of turns. For example, a 17-turn triple-wind motor has a set of three wires wound together around each armature pole 17 times.
Commutator
The commutator is part of the armature, and is responsible for controlling the flow of current to the windings on the different armature poles. As the armature rotates, different poles in sequence receive current. As each pole is energized, it temporarily becomes a magnet, which is then attracted or repelled by the permanent magnets in the motor. It is this constant changing of which poles are magnetized that causes the motor to rotate.
Brushes
The brushes supply the current to the commutator. As the armature turns, the stationary brushes slide over the different commutator segments in turn. Most motors have two brushes, although some of the larger motors may have four or more. Because of the constant friction, brushes eventually wear out. Except in the cheapest of motors, the brushes are readily replaceable.
Timing
Timing is the process of adjusting the position of the brushes relative to the motor’s magnets to optimize the time at which the commutator switches the current from one armature pole to the next. Inexpensive motors cannot be timed. Those that can be should be adjusted according to the manufacturer’s recommendations.
Brushless Motor
A brushless motor is one in which the windings are inside the motor case, and the magnets are on the armature. Since there is no need for current to reach the rotating armature, there is no commutator, and no brushes are needed. Instead, the windings are energized sequentially by a special electronic controller.
Suppression Capacitors
Non-brushless electric motors generate electrical noise as the brushes alternately make and break contact with the various commutator segments. To keep this noise from getting back to the speed control and/or radio receiver, capacitors are installed on the motor connections. These capacitors are usually supplied with, or preinstalled in, the motor.
Motor Control
Electronic Speed Control (ESC)
This is an electric aircraft’s throttle. It works by turning the power to the motor on and off at a high rate. The motor "sees" an average voltage based on the percentage of the time the power is on.
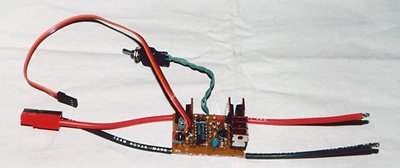
A home made electronic speed control (from the July 1999 issue). On the right are the leads to the motor. The arming switch is on the end of the twisted wires at the top. A pair of Sermos connectors terminates the battery leads.
High vs. Low Rate
In the early days of electric flight, speed controls switched motor power on and off at the same rate that the transmitter sent control pulses to the receiver, usually about 50 times per second. This resulted in very inefficient motor operation at partial throttle, often causing overheating and permanent weakening of the motor’s magnets. Modern speed controls switch the motor at a much higher rate, usually about 1,000 to 3,000 times per second, and do not cause such problems.
Freewheeling Diode
This is a diode that is connected across the motor’s terminals (or across the output of the speed control), to recirculate current through the motor during the off-times of the speed control’s cycle. This serves to increase speed control efficiency, and also provides some noise suppression. Most modern speed controls have this diode already installed, but some require you to solder it to the motor itself.
Current Rating
A speed control can handle only a certain amount of current before it overheats. They are generally rated by the amount of current they can handle continuously, and sometimes also by a maximum current they can handle for a few seconds. It is important to select a speed control whose current rating is at least as high as the current your motor will draw at full throttle.
Arming Switch
An arming switch prevents the speed control from applying power to the motor before you want it to (for example, if the receiver picks up a signal from another transmitter on your frequency). Many modern speed controls don’t have an arming switch. Instead, they will not arm until they have first received a throttle-off signal for a few seconds.
Brake
When power is removed from an electric motor, it keeps spinning on its own for a while. This is especially true when there is a propeller attached, and the plane is moving through the air, in which case the motor simply won’t stop, and will act as a generator instead. A brake works by connecting the motor terminals together, making the generator work harder. The idea is to make it work so hard that it stop. If you are using a folding propeller, it can then fold. The brake is a feature built into many speed controls.
Battery Eliminator Circuit (BEC)
A BEC (often pronounced "beck") provides power to your plane’s radio system from the motor battery, instead of requiring you to install a separate radio battery. In a small plane, this can save a significant amount of weight. BECs generally have limits as to the number of cells and/or servos you can use.
Cutoff and Restart
If your ESC has a BEC, it should also have a cutoff circuit so that it will cut power to the motor when the battery is about to run down too far to reliably power the radio system. If your ESC doesn’t have cutoff, you could run the motor battery down so far that your receiver stops working, at which point you’ll lose control. Some ESCs allow you to restart the motor for a few seconds after cutoff to provide power if you have to go around.
Optoisolator
In an attempt to prevent electrical noise from the motor from flowing back into the receiver and causing interference, some ESCs use an optoisolator chip. This makes the connection between the receiver and the ESC using light instead of current (this is all done inside the chip). This makes it impossible for noise to get to the receiver via the ESC. Unfortunately, optoisolation cannot be used in conjunction with a BEC (well it can, but would be pointless) because the BEC must provide power to the receiver from the same source as the ESC powers the motor.
Sensorless
This term applies only to ESCs for brushless motors. Because a brushless motor relies on electronics for switching the windings on and off, the controller must know the position of the armature shaft and its magnets. Many brushless motors have sensors in them that feed this information back to the ESC. Some brushless ESCs don’t need these sensors, and instead detect the armature position by carefully monitoring the currents flowing through the power wires. Such controls are called sensorless.
Fuse
A fuse interrupts the flow of electricity if the current gets too high. This can happen, for instance, if the propeller becomes stuck (because of contact with the ground). By blowing, the fuse protects the motor and speed control from damage, and prevents a fire. The most commonly used fuse in electric models is the automobile blade type. Pick a fuse whose rating is just slightly higher than the current at which you expect the motor to run.
Connector
Connectors are used to connect the battery to the speed control, and by some modelers, the speed control to the motor. A poor connector has a high resistance and will reduce efficiency, so it’s worthwhile to use the best quality connectors.
Transistor
A transistor is the electrical equivalent of a valve. Just like a water valve allows a small force (such as a person turning a tap) to control a large force (such as water through a dam), a transistor allows a small current (for instance, from within the circuitry of a speed control) to control a large current (such as current flowing to the motor). There are many different kinds of transistors. The most common is the bipolar transistor, but these are not used in speed controls these days.
MOSFET or FET
The term MOSFET, usually pronounced "moss-fett" is short for Metal Oxide Semiconductor Field Effect Transistor. A field effect transistor, or FET, is just one form of transistor technology, and a MOSFET is just a particular way of constructing a FET. FETs have the property that changing the voltage on the input (the "gate" lead) affects the resistance between the two output leads ("source" and "drain"). Modern MOSFETs have very low "on-resistance", meaning they can conduct large amounts of current without significant voltage and power losses. Remember that V = IR, and P = IV, so if R is lower, V will be lower for a given current, I, and if V is lower, P will be lower.
Integrated Circuit
An integrated circuit is a collection of electronic components (resistors, capacitors, transistors) on one common piece of silicon, all encased in a small package with several external connections. Some integrated circuits provide functionality needed in a wide variety of applications (for example, a voltage comparator or an amplifier), while others are specific to a single task (such as a servo amplifier or peak-detecting NiCd charger). Integrated circuits are often referred to as "chips". Without integrated circuits, a typical speed control would require about a hundred separate components.
Embedded Controller
An embedded controller, or microcontroller, is a single chip containing all the components making up a computer, including a central processing unit (CPU), random access memory (RAM), read-only-memory (ROM), and input/output (I/O) ports. Such computers are not intended for general purpose use (such as the one on your desk), but rather for use inside other equipment (camcorder, cellular phone, calculator, NiCd charger, speed control, etc.). Using an embedded controller reduces a speed control to just one chip, some MOSFETs, and very few additional components. All the features of the control, such as soft start, BEC cut-off, arming, adjusting to the characteristics of your transmitter, and so on, are then implemented as software. A commonly used embedded controller is the PIC series, from the company Microchip.
Hall Sensor
Brushless speed controls that are not sensorless need some sort of sensor to detect the position of the motor shaft as it rotates. Most commonly, these are Hall sensors. A Hall sensor uses a phenomenon known as the Hall effect to detect magnetic fields. Since the shaft of the brushless motor contains the motor’s magnets, a Hall sensor is a simple way of detecting where the shaft is in its rotation.
The Power Supply
Next issue, I will talk about the terminology of the all-important battery, without which our electric planes would go nowhere (no extension-cord jokes please).
In the mean time, if there are any other terms you’d like to see definitions for, please e-mail me.
Related Articles
If you've found this article useful, you may also be interested in:
- Measuring Up
- Let’s Do the Twist
- How Electric Motors Work
- More Electric Flight Terms
- Electromagnetic Interference Reduction

If you've found this article useful, consider leaving a donation in Stefan's memory to help support stefanv.com
Disclaimer: Although every effort has been made to ensure accuracy and reliability, the information on this web page is presented without warranty of any kind, and Stefan Vorkoetter assumes no liability for direct or consequential damages caused by its use. It is up to you, the reader, to determine the suitability of, and assume responsibility for, the use of this information. Links to Amazon.com merchandise are provided in association with Amazon.com. Links to eBay searches are provided in association with the eBay partner network.
Copyright: All materials on this web site, including the text, images, and mark-up, are Copyright © 2025 by Stefan Vorkoetter unless otherwise noted. All rights reserved. Unauthorized duplication prohibited. You may link to this site or pages within it, but you may not link directly to images on this site, and you may not copy any material from this site to another web site or other publication without express written permission. You may make copies for your own personal use.