Build a Versatile Miniature High-Rate ESC with BEC and Brake
July 1, 1999 for Sailplane & Electric Modeler Magazine
This electronic speed control (ESC) for brushed motors combines the features of two of my earlier designs. One was a high-rate 30A ESC with a brake, and the other a high-rate 12A ESC with a BEC (receiver battery eliminator circuit).
This ESC is an analog one, using off-the-shelf components. There are no microprocessors (which would require specialized equipment to program), and no surface-mount parts. It’s not as small or as light as many commercially available ESCs, but it’s smaller than many other do-it-yourself designs. It’s also versatile, in that it can be built for many applications, ranging from small Speed 400 sport planes to "hot liner" sailplanes.
Specifications
This ESC has the following technical specifications (if built exactly as described):
- 6 to 12 cell operation.
- Size: 1.9" L x 1.3" W x 0.7" H (48mm x 33mm x 15mm).
- Weight: approximately 1 ounce (28g) without motor and battery leads.
- High-rate switching (1,500 Hz).
- Current: 48A continuous, 72A for 30 seconds.
- On resistance: 0.003Ω.
- Typical voltage or power loss: 52mV or 1.6W @ 30A.
- Battery eliminator circuit (BEC) on 6 to 10 cells.
- Soft start and soft brake.
- Arming/power switch.
Furthermore, there is no momentary burst of power when you first switch on as there is with some older analog designs, and the power stays off if the transmitter is off (unless another transmitter is operating on your frequency, or you’re using a PCM receiver and your failsafe doesn’t go to zero throttle).
How it Works
Figure 1 is a schematic diagram of the ESC. The main component is Z1, an LM339 quad voltage comparator IC. As its name indicates, this chip contains four independent voltage comparators, Z1A through Z1D. These have what is known as an open-collector output, which means they can be either low (near 0V), or floating (effectively disconnected). To go to a high voltage, a pull-up resistor is needed.
Z1A acts as an input buffer, isolating the rest of the ESC from variations between brands of receivers. R2 is a pull-down resistor which ensures that the ESC is off if no receiver is connected. R3 and R4 form a voltage divider, giving about 1.6V at pin 4 of Z1A. If the input signal is higher than this (as it is during a pulse), pin 2 goes to 5V thanks to R5. If the input signal is below 1.6V (between pulses), pin 2 goes to 0V.
D1, R6, R7, and C1 form an integrator, which smoothes the pulsing on-off signal from Z1A into a fairly steady voltage, which appears at pin 9 of Z1B. This voltage will vary from about 1.15V to 1.65V depending on the throttle stick position. Because of this smoothing action, the integrator takes some time to respond to changes in throttle stick position. For example, if you move the stick from off to full-throttle, it will take the ESC about one second to go to full throttle. You can use this ESC as a soft-start switch by controlling it with a switch-operated channel.
Z1C, together with C2 and R8 through R12, form a triangle wave generator. The triangle wave appears at pin 10, and oscillates between about 1.2V and 1.6V, depending on the setting of R12. The frequency also depends somewhat on R12, but is approximately 1,500Hz.
Going back to Z1B, we see that the triangle wave from Z1C is compared to the integrated voltage. When the integrator voltage is higher than the triangle wave, pin 14 is pulled to the motor battery voltage by R15. When the integrator voltage is lower than the triangle wave, pin 14 goes to 0V. The percentage of time that the integrator voltage exceeds the triangle wave depends on the setting of the throttle.
The output from pin 14 is used to drive N-channel MOSFETs Q1 through Q4 via resistors R17 through R20, which serve to ensure that the gate current is divided equally among the MOSFETs so they all turn on at the same rate.
Everything described so far constitutes a simple high-rate ESC with no BEC or brake.
The LM2940CT-5 is a low-dropout 5V regulator. Low-dropout means that the input voltage doesn’t have to exceed the output voltage (5V) by much in order for it to work. C3 and C4 filter the voltage coming from the motor battery (which can be quite electrically noisy due to motor noise). C5 stabilizes the voltage regulator (it won’t work correctly without it), and C6 provides some extra filtering on the 5V line. The 5V from the regulator is used to power the rest of the ESC, and also the receiver and servos.
Z1D compares a fraction (set by R14) of the motor battery voltage against a fixed reference of 1.6V. If the fractional battery voltage drops below 1.6V, the output of Z1D (pin 1) goes to 0V, and through R21 and D2, pulls the input of Z1B to about 0.7V. This in turn causes pin 14 to go to 0V, thus shutting off the motor. R13 provides positive feedback to prevent the motor from turning back on as soon as the voltage goes back up (which it will when the load of the motor is removed from the battery).
D3, C7, R16, and Q5 form the brake. Whenever Z1B’s pin 14 is high (due to R15), current flows through D3, bringing the input to Q5 high. Q5 is a P-channel MOSFET, which is off when it’s input is high. During the times that pin 14 is low, no current flows through D3, but the high input to Q5 is "remembered" by C7. As long as there is any throttle activity, C7 will keep being "reminded" about 1,500 times per second. However, once the throttle is off for a while, C7 will slowly "forget" as it becomes charged via R16. This will take about 1/10th of a second. Once the input to Q5 goes low, it will turn on, effectively shorting out the motor and hence acting as a brake. Q5 turns on somewhat gradually, and it’s resistance is rather high compared to the other MOSFETs, so the brake is quite soft.
D4 is the freewheeling diode, which serves to circulate motor current during the times that Q1 through Q4 are off, greatly improving efficiency at part throttle. D4 also protects the MOSFETs from motor noise.
Finally, S1 is the combination arming and power switch. When S1 is open, no power is applied to the voltage regulator, so nothing happens in the ESC. Furthermore, there is no voltage by which R15 can pull Z1B pin 14 high, so the FETs cannot turn on. R16 of the brake helps ensure that pin 14 remains low. If you wish, you can install a separate high-current switch in one of the motor leads for additional protection.
Not shown, but very important, is a fuse. This should go into the MOTOR+ lead (i.e. between the ESC and the motor). Do not put it in the BATT+ lead between the battery and ESC, because if it blows, the BEC will cease to function and you will lose control of your airplane.
Construction
The ESC is best built on a printed circuit board. My article, Making Excellent Printed Circuit Boards, gives tips on etching your own boards. Figure 2 shows the board layout from the copper side, actual size (1.9" x 1.3", or 48mm x 33mm).
Figure 3 is an enlarged view showing the component locations as viewed from the component side.
First, install all the fixed resistors. Install R1 to R11, R13, R15, and R21, and R22 to R23 standing up over one hole, with the other lead bent over and going down into the other hole. R16 to R20 lay down flat on the board (you’ll have to bend the leads very close to the resistor bodies to make them fit). When you install R5, also install jumper J2, since it shares a hole with R5. Likewise, when installing R21, also install J1.
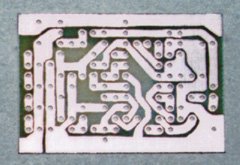
The printed circuit board after etching. The traces aren’t as straight as they are in Figure 2 above because they were transferred to the board by hand, using an etch-resist pen.
Next, install jumper J3, variable resistors R12 and R14, and a 14-pin socket for Z1 (you don’t have to use a socket, but I suggest you do since it is hard to unsolder a defective chip).
Install all the capacitors. Be sure to observe the polarity for C1, C3, and C5; their + leads are marked on the component layout diagram. Note that capacitor C8 is installed differently from all the rest. Rather than being installed into holes in the circuit board, it is soldered directly to the two outside legs of variable resistor R14.
Next, install diodes D1 to D3, observing their polarity. Install D3 with its banded end on the board, next to C7. The banded end of D1 and D2 should be oriented as shown in the component layout diagram. When you install D2, also install jumper J1, since it shares a hole with D2.
The next components to install are the drive MOSFETs, Q1 to Q4. These should be installed with their tabs towards the BATT-/MOTOR- side of the board (the bottom of the component layout diagram). Before soldering, the drain and source leads of each MOSFET should be bent over towards the BATT-/MOTOR- side of the board, so that they reach the corresponding leads of the next MOSFET (or the edge of the board for Q1). This will help distribute motor current more evenly between the MOSFETs, since the copper trace alone is not heavy enough to carry this much current without significant losses.
Next install Q5 and D4, which should have their tabs away from each other. Note that D4, although it looks just like a MOSFET, has only two leads.
Finally install VR1, which should be installed with its tab towards the MOSFET end of the board (i.e. facing the same way as D4).
If you’re unsure about any of the above, please refer to the component layout diagram and the photos of the completed ESC.
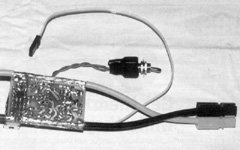
Bottom view of the speed control. Notice that the BATT+/MOTOR+ lead (top) is one continuous wire, whereas BATT- and MOTOR- (bottom) are two separate wires.
Cut a 12" (305mm) piece of red 12ga (3.3mm2) or 13ga (2.6mm2) flexible wire. With a hobby knife, remove about 1.9" (48mm) of insulation from the middle of the wire. Tin this with a heavy soldering iron (at least 45W). Also thoroughly coat with solder the BATT+/MOTOR+ trace on the circuit board. Lay the bare section of the wire on the trace, and clip it down at each end with alligator clips. Run the soldering iron slowly along the wire, allowing it to melt the solder in the wire and on the board. The wire should fuse to the trace along the whole length of the board.
Cut a 6½" (165mm) piece of black 12ga or 13ga wire and strip 1.6" (40mm) of insulation from one end and tin it. Coat the BATT- trace with solder, and solder the wire along its length as described above. Then cut a 5½" (140mm) piece of black 12ga or 13ga wire and strip 0.2" (5mm) of insulation from one end and tin it. Coat the MOTOR- trace with solder, and solder the wire to it.
Install the appropriate connectors on the BATT leads. If you prefer connectors between your ESC and motor as well, install them on the MOTOR leads.
Attach the receiver lead to the CH+, CH-, and SIG pads. The CH+ lead is usually red, the CH- lead is usually black or brown, and the SIG lead is usually white, orange, or yellow. The colors vary with the brand of receiver lead you purchased.
Connect the arming switch to the S1 pads on the board using short lengths of thin (22ga or 24ga) flexible wire.
Testing and Adjustments
Double check all your work, making sure all the components are installed the right way around, and that you haven’t inadvertently created any solder bridges between traces. A magnifying glass helps here. Do not insert Z1 into it’s socket yet.
Connect a 6 to 10 cell motor battery to the BATT leads and turn on the arming/power switch. Check that there are no high voltages on the receiver lead (measure between the CH- and the SIG leads). Also check that there is 5V between the CH- and CH+ leads.
Turn off the arming switch, disconnect the power, and install Z1 into its socket (the IC will have a semi-circular notch or small dot at the pin 1 end). Turn R14 fully counter-clockwise to disable the low-voltage cut-off, and turn R12 fully counter-clockwise to disable the triangle wave oscillator.
Attach a motor, without a propeller, to the MOTOR leads. Make sure the motor is restrained so it cannot move. Plug the receiver lead into your receiver’s throttle channel, and reconnect the motor battery.
Turn everything on, in the following order: throttle stick off, transmitter on, arming switch on. If the motor starts, turn off the arming switch immediately and reinspect the board for errors.
Now slowly turn R12 clockwise until the motor begins to whine. When you reach that point, turn R12 counter-clockwise slightly until the whine stops. If you advance the throttle, the motor should start, with the speed proportional to how far you’ve moved the stick. The speed of the motor should increase as you move the stick forward. It should stop increasing before you reach full throttle. Once you reach full throttle, move the throttle trim forward to confirm that the motor won’t go any faster.
If moving the trim lever at full throttle does increase the motor speed, then you aren’t getting the full range of control. Some transmitters have stops on the throttle stick; check that the throttle stick has the same range of travel as the elevator stick. If your transmitter has such stops, you can open it up and remove them. If you still don’t get full throttle range, replace R9 with a higher valued resistor (82kΩ or even 100kΩ).
If at any point during the testing and adjustment procedure, something doesn’t work the way it should, please refer to the troubleshooting section at the end of this article.
Low Voltage Cut-off Adjustment
The low voltage cut-off level is set by R14. The desired cut-off voltage should be about 0.7V to 1.0V per cell, depending on the type of cells you are using and the current level at which you are operating. The following table suggests some per-cell cut-off voltages:
600AE/500AR | 800AR/2000SCE | 1700SCR/RC2000 | |
---|---|---|---|
10A |
0.80V |
0.90V |
1.0V |
20A |
– |
0.80V |
0.9V |
30A |
– |
– |
0.8V |
40A |
– |
– |
0.7V |
Multiply the desired per-cell cut-off voltage by the number of cells. For example, if you intend to draw 30A from a 7-cell RC2000 pack, your cut-off voltage would be 7 x 0.8V, or 5.6V.
Now, measure the voltage of a charged battery pack with the same number of cells (7 in our example). This will be your reference pack. Multiply this voltage by 1.6, and divide by the desired cut-off voltage to get an adjustment reference voltage. For example, if your pack reads 9.0V, and your cut-off voltage is to be 5.6V, the adjustment reference voltage would be 9.0 x 1.6 / 5.6, or 2.57V.
To adjust the cut-off voltage, connect a voltmeter between BATT- and the center terminal of R14 (or pin 7 of Z1). Connect the reference pack to the ESC, turn on your transmitter, set the throttle to off, and turn on the arming switch. Turn R14 fully counter-clockwise, and then slowly turn it clockwise until the voltmeter shows the adjustment reference voltage (2.57V in the example above).
After setting the cut-off voltage, bench test the entire system and confirm that the cut-off is activated when the battery reaches the desired voltage.
BEC Limitations
The BEC functionality is provided by the LM2940CT-5 regulator, which provides 5V from the motor battery for use by the receiver and servos. However, the difference in voltage between the motor battery and 5V, multiplied by the current drawn, must be dissipated by the regulator as heat. For instance, if your motor battery is at 9V, and your radio equipment is drawing 200mA (0.2A), the regulator must dissipate (9V – 5V) x 0.2A = 0.8W. With higher battery voltage and/or higher currents, the power dissipated by the regulator increases. With adequate cooling air, the 2940 can dissipate about 1.5W of heat. This limits the motor battery voltage and current that can be handled, as summarized in the following chart:
Number of Cells | Maximum BEC Current |
---|---|
6 |
0.7A |
7 |
0.4A |
8 |
0.3A |
9 |
0.25A |
10 |
0.2A |
Use this chart and the information provided with your radio to determine the maximum number of servos that can be operated from the BEC. A typical system with a receiver and two micro-servos draws under 0.3A average, but can draw up to 1A under strenuous conditions. Make sure that all the control surfaces and pushrods move freely, without binding. Remember, if the BEC overheats, it will shut down, and you will lose control of your plane.
Modifications
As I mentioned in the introduction, this ESC is very versatile. You can omit or substitute various components depending on your requirements.
BEC Modifications
If you will be using 8 to 10 cells, you can use the less expensive LM7805 voltage regulator in place of the LM2940CT-5. This regulator requires at least 7.5V input to produce 5V, so be sure to set the cut-off to 7.5V or higher.
If you do not need BEC, you can omit VR1, C3, C4, C5, and C6. The rest of the circuitry will then be powered by your receiver battery via the CH+ lead.
You can disable the automatic low voltage cut-off by omitting R13, R14, R21, R22, C8, and D2. You should however then install a jumper between the top two holes shown for R14 in the component layout diagram to keep Z1D from oscillating.
Using the component values indicated, the BEC will completely shut down the motor when the battery drops below the cut-off level. If you increase R13 from 100KΩ to 150KΩ, the BEC will pulse the motor on and off for a while before shutting it down completely.
Brake Modifications
The brake can be made softer by using a higher resistance MOSFET, such as the IRF9530. With this MOSFET, the brake will probably not be strong enough to stop a direct-drive propeller.
If you don’t need a brake at all, you can omit C7 and Q5. Do not omit D3 and R16, as these are needed to ensure the ESC stays off when not armed.
Drive MOSFET Modifications
You don’t need to install all four of the drive MOSFETs (Q1 to Q4) and their corresponding gate resistors (R17 to R20). Each IRL2203N MOSFET can handle about 12A, so you can select the number of MOSFETs according to your current handling requirements. For a single Speed 400 motor, one MOSFET that can handle at least 10A would be sufficient. You can also use much thinner wire for the motor and battery leads (e.g. 16ga, or 1.3mm2).
You can also substitute different types of MOSFETs for the IRL2203N specified (but you must use all the same type on one ESC). The following table lists some possible substitutions, the minimum number of cells required, and the current handling capabilities per MOSFET:
MOSFET | Minimum Cells | Current per MOSFET |
---|---|---|
IRL3803N |
6 |
13A |
IRL2203N, SMP60N03-10L |
6 |
12A |
IRL3103 |
6 |
10A |
SMP60N06-14 |
7 |
10A |
SMP60N06-18 |
7 |
9A |
IRLZ44N, ECG2986 |
6 |
8A |
IRL3303 |
6 |
7A |
IRFZ40, IRFZ44, SMP50N06-25, ECG2395 |
7 |
7A |
BUZ11 |
8 |
7A |
SMP25N05-45L |
6 |
5A |
Not all of the above are ideal for ESC use, but I’ve found that in some parts of the world, it’s difficult to get some of the more modern MOSFETs, so less-than-ideal parts are sometimes the only choice.
The current ratings above assume reasonable cooling airflow and no covering over the ESC. Under these conditions the MOSFETs can readily dissipate about 1.5W each. If choosing a different MOSFET, keep the power dissipation (current squared times on-resistance) below 1.5W.
Installation
Install the ESC in the plane near the motor, keeping the motor leads as short as possible. Make sure the ESC circuit board doesn’t touch anything metallic. Be sure to install interference suppression capacitors on the motor (a 0.1µF capacitor across the motor terminals, and a 0.047µF capacitor between each motor terminal and the motor case).
If you are using the BEC feature, install a fuse in one of the motor leads. If you are not using the BEC, install the fuse in one of the battery leads. For a fuse holder, I generally use two 14ga female spade connectors soldered at right angles to the wires, and insulated from one another with heat-shrinkable tubing.
Before flying, do a range check, both with the motor off, and with the motor running at various throttle settings. You should get at least 80-100ft (24-30m) range with the radio antenna down.
Notes
There are a few things you should know about the operation of this ESC.
The first thing you’ll probably notice is that response to throttle changes is not instantaneous. For example, going from off to full-throttle takes about one second. This is because it takes time for the integrator (R6, R7, and C1) to respond to changes in the pulse width from the receiver. Replacing C1 with a 1µF capacitor will result in faster response, but noisier operation.
Moving other controls, such as the rudder, will momentarily affect the throttle setting by a few percent. This is because during the movement of a control stick, the time between throttle pulses can vary, and the integrator is thrown off by this. This effect is minimal though. If the throttle level changes a lot during control movements, it’s likely you have a binding control surface which is causing high current drain from the BEC or receiver battery, which can adversely affect the operation of the ESC.
If you are using the ESC to operate two or more motors at once, you should install a Schottky diode on each motor. Suitable diodes can be obtained from your local hobby shop (they’re sold for R/C car use). The diode should be installed across the terminals, with its banded end at the positive motor terminal.
Troubleshooting
If you can’t get the ESC to work as built, use the following as a guideline for troubleshooting. Refer to the How it Works section to understand what is supposed to happen. A basic understanding of electronics would be helpful here. But don’t panic; the most common of problems are found by following step 1 below.
- Check for solder bridges between traces on the board. If that checks out, look at all the components, and make sure they are the correct ones. For the diodes, MOSFETs, tantalum capacitors, and Z1, make sure they are installed the right way around. If everything looks right, proceed with the steps below.
- Check that the BEC is working (unless you’ve omitted the BEC and are using a receiver battery). Measure the voltage between BATT- and CH+ (connect a voltmeter’s black lead to BATT- and the red lead to CH+). With BEC, it should read about 5V. With a receiver battery, it should be between 4.8V and 5.6V or so, depending on the state of charge of the battery.
- Move the red voltmeter lead to Z1 pin 1. The voltage should be above 1.6V. If it is less than this, check the setting of R14 as described under Low Voltage Cut-off Adjustment, and check the wiring to Z1D and all the associated components.
- Move the voltmeter’s red lead to Z1 pin 9. Make sure the voltage varies as you move the transmitter throttle stick. It should vary between about 1.15 and 1.65V. If it does, the input stage is fine. If not, check the wiring to Z1A and all the associated components.
- Check that the oscillator is working. Move the voltmeter’s red lead to Z1 pin 10 (or pin 8). This should read about 1.4V. If it doesn’t, adjust R12 until it does. If that works, the oscillator is probably fine. If it doesn’t work, check the wiring to Z1C and all the associated components.
- Move the red lead of the voltmeter to pin 14 of Z1. With the arming switch on, the voltage should vary between 0V and the battery voltage as you move the throttle stick. If that works, the control circuitry is fine. If it doesn’t work, check the wiring to Z1B, all the associated components, and the arming switch
If everything is okay up to this point, the problem must be with the FETs. Assuming they are all installed correctly, it might be best to remove them all, and reinstall them one at a time, using a small motor (such as a Speed 400 7.2V with a 6×3 propeller) to test the ESC after each FET is installed.
Parts List
The following table lists all the parts along with DigiKey part numbers. Radio Shack part numbers are also shown for those parts available at your local Radio Shack store.
Part | Description | DigiKey Part | Radio Shack Part |
---|---|---|---|
R1, R3 |
10kΩ ¼W resistor |
10KQBK-ND |
271-1335 |
R2, R16 |
470kΩ ¼W resistor |
470KQBK-ND |
271-1354 |
R4, R5 |
4.7kΩ ¼W resistor |
4.7KQBK-ND |
271-1330 |
R10, R15 |
1kΩ ¼W resistor |
1.0KQBK-ND |
271-1321 |
R6 |
220kΩ ¼W resistor |
220KQBK-ND |
271-1350 |
R7 |
39kΩ ¼W resistor |
39KQBK-ND |
|
R8 |
22kΩ ¼W resistor |
22KQBK-ND |
271-1339 |
R9 |
75kΩ ¼W resistor |
75KQBK-ND |
|
R11 |
68kΩ ¼W resistor |
68KQBK-ND |
|
R12 |
10kΩ trimmer |
3316F-103-ND |
271-282 |
R13 |
100kΩ ¼W resistor |
100KQBK-ND |
271-1347 |
R14 |
47kΩ trimmer (or 50kΩ) |
3316F-503-ND |
271-283 |
R17, R18, R19, R20, R21 |
100Ω ¼W resistor |
100QBK-ND |
271-1311 |
R22 |
47kΩ ¼W resistor |
47KQBK-ND |
271-1342 |
R23 |
1MΩ ¼W resistor |
1.0MQBK-ND |
271-1356 |
C1 |
2.2µF 10V tantalum capacitor |
P2022-ND |
272-1435 |
C2 |
22nF capacitor |
P4953-ND |
|
C3 |
10µF 25V tantalum capacitor |
P2049-ND |
272-1025 (electrolytic) |
C4, C6, C7, C8 |
0.1µF capacitor |
P4923-ND |
272-109 |
C5 |
47µF 10V tantalum capacitor |
P2030-ND |
272-1027 (electrolytic) |
D1, D2, D3 |
1N914 or 1N4148 diode |
1N4148DICT-ND |
276-1122 |
D4 |
MBR1645 Schottky diode |
MBR1645-ND |
|
Q1, Q2, Q3, Q4 |
IRL2203N MOSFET |
IRL2203N-ND |
|
Q5 |
IRF9Z34N MOSFET |
IRF9Z34N-ND |
|
Z1 |
LM339 quad comparator |
LM339N-ND |
276-1712 |
VR1 |
LM2940CT-5 regulator |
LM2940CT-5.0-ND |
|
S1 |
SPST mini toggle switch |
CKN1003-ND |
275-624 |
Addendum
Since the original article was written, much has changed in electric flight, with the two most significant advances being the widespread adoption of brushless motors and the introduction of LiPo cells. If you’ve switched completely to brushless, then you probably aren’t using this speed control any more, but if you’ve still got some brushed motor power systems and want to use them with LiPo packs, here are the relevant specifications for this ESC:
- Works with 2 to 4 series LiPo cells (i.e. 2S to 4S).
- 48A continuous, 72A for 30 seconds.
- Battery eliminator circuit (BEC) when used with 2 or 3 series LiPo cells.
The number of parallel cells doesn’t matter, so long as the power system doesn’t exceed the ESC’s current limits. Just be sure to adjust the cut-off voltage (as described in the article) appropriately so that the cells are not discharged below 3V per cell (i.e. 6, 9, or 12V).
Related Articles
If you've found this article useful, you may also be interested in:
- BattMan II: Computer Controlled Battery Manager
- LED Bargraph Optical Tachometer
- On/Off Motor Controller with Brake
- High Speed NiCd Charger for Electric R/C
- Analog Bar Graph Expanded Scale Voltmeter
- Miniature High-Rate Speed Control with Battery Eliminator Circuit (BEC)
- Miniature High-Rate Speed Control with Brake
- Getting the Most from Your Radio Control System
- Low Cost Thermal Peak Detection NiCd Charger

If you've found this article useful, consider leaving a donation in Stefan's memory to help support stefanv.com
Disclaimer: Although every effort has been made to ensure accuracy and reliability, the information on this web page is presented without warranty of any kind, and Stefan Vorkoetter assumes no liability for direct or consequential damages caused by its use. It is up to you, the reader, to determine the suitability of, and assume responsibility for, the use of this information. Links to Amazon.com merchandise are provided in association with Amazon.com. Links to eBay searches are provided in association with the eBay partner network.
Copyright: All materials on this web site, including the text, images, and mark-up, are Copyright © 2024 by Stefan Vorkoetter unless otherwise noted. All rights reserved. Unauthorized duplication prohibited. You may link to this site or pages within it, but you may not link directly to images on this site, and you may not copy any material from this site to another web site or other publication without express written permission. You may make copies for your own personal use.
Anonymous
October 12, 2008
Awsome
Bruno
October 22, 2008
hi, i’m searching for a R/C circuit to control the speed of 2 motors but i only get circuits wich make my project(a R/C boat) go foward-back and left-right (the convencional transmitter/receiver 27MHz) … Can you help me get one electronic circuit with variable voltage to control the speed of the motors with 2 potenciometers? is a project for school and it’s very important. tank you very much and sorry about my english… Bruno, Portugal
Peter Paul Punzalan
August 16, 2010
thanks for sharing!this will help me a lot!
devendra
September 01, 2010
can this circuit be used for regenerative braking?
Stefan Vorkoetter
September 02, 2010
Sorry, this circuit can’t do regenerative braking. It just does resistive braking.
Ashro Gopal
January 19, 2011
well this info is for brushed motors and it is pretty nice . if possible let me know about brushless also. thanks
Yunizo Tatoo
August 26, 2011
I have a power sliding enegia 1 to 15 volts have a brushless motor I would like to adapt the engine in a tattoo machine. how do I make the source of energy to move a brushless motor? Please help me!
Melandro Villedo
September 08, 2011
I need diagrams ESC with reverse
Anas W. Ata'a
October 14, 2011
nice work.
Daniel Farley
February 03, 2012
good work, I’m looking to make a brsuhless I see controlled esc but I enjoyed reaing your article and its bookmarked for if I find a brushed motor kicking around one day.
thanks
omkar
May 04, 2012
hello,
r u selling this board. i need it.
zero
September 01, 2012
Sir I am looking for a analog speed controller with reverse, brake is not needed since i will be having mechanical brake for the drift car..I am hoping you can help me because it has been an endless search..
peyman
April 04, 2013
very useful esc circuit in net
I need Fm 4ch radio shematic, rf or infra-red
thanks
Akash
October 20, 2013
Hello, actually I’m facing a problem with my 30A brushless esc. t was working fine, but suddenly, the motor started jerking, at the middle of throttle. i immediately turned off the power to check t again. then, i connected the circuit back again, this time, there was very faint beeping sound by esc. when i started giving throttle, again it was jerking. i reconnected the circuit, twice or thrice again, by changing the motor pins, checking receiver and all, but now it was not at all beeping and continuously jerking the motor rotation. let me tell you, the receiver is working fine, and the there is no fault with the motor as well, as i have checked them with another esc. can u please help me explaining what exactly is the problem with it and help me eliminating it??
Matan
October 29, 2014
Hi, I am building a small generator which I want to use to power a ground station and to charge batteries. I am using a gas engine and brushless motor and a rectifier. I want to connect an esc to spin the brushless motor(the generator) to start the gas engine. My question is if there any problem with it?the esc can be burned when the gas engain will start? Any current can go back into the esc and burn it? The generator can “do” his job when the esc is steel connected?
Thank you!
Christiaan
February 23, 2016
Wow!
This must definitely one of the most well presented “how to” articles that I’ve seen on this subject. Many thanks Stefan, I will be using this for the basis of a speed controller for an electric kayak. (12V trolling motor, I need maximum 30A)
Regards,
Christiaan
coker
March 25, 2016
sir please can you make a video on all this steps, i have been looking for this years back.. you are my mentor
Aditya
November 11, 2016
sir please tel me how many volts required for this ckt working on battery leads
Stefan Vorkoetter
November 11, 2016
It will work with 7.2 to 14.4 Volts.
bheema
March 18, 2017
Where is -CH in circuit.
Stefan Vorkoetter
March 18, 2017
I seem to have omitted showing that in the schematic. CH-, BATT-, and all the ground symbols are all connected together.
badix08
September 29, 2017
Hi Stefan, how to make it support the reverse ?
Thanks
Chase
January 11, 2019
Hi Stefan,
I am a hobbyist trying to build a large scale RC car with an Arduino. I have managed to get everything working and currently control the motor with PWM via some power mosfets but cannot find or figure out anyway to reverse the motor without using relays which will eventually burn out. Long story short, Is there a way to incorporate Bi-Directional control with your above design? Your input would be highly appreciated!
Regards!
Stefan Vorkoetter
January 11, 2019
There are basically two ways to achieve reversing. One is to use relays, and the other is to use two pairs of MOSFETs (Google “H-bridge”). The relay is the simpler solution, and will work fine, and won’t burn out unless you shift direction while power is applied to the motor. Since you’re controlling it from software, you can make sure this never happens. (The MOSFET H-bridge has potential for damage too if you activate both pairs at once.)
الکترونیک
September 21, 2019
Hi,very useful esc circuit in net
I need Fm 4ch radio shematic, rf or infra-red
thanks.
thomas
November 17, 2019
Hello ,
do you think this esc is usable in an onroad car with a mabuchi rs540 27Turns motor . and is it brake function proportional too with stick movenment ? thanks thomas
Stefan Vorkoetter
November 17, 2019
It will work in a car, but it has no reverse, and the brake comes on fully as soon as the throttle is reduced to zero. There is no proportional braking. So it’s probably not what you want.